THE ORIGIN
In the sixties, economic output in Europe, the US and Japan boosted paper consumption with advertising, newspaper printing, packaging and labelling all contributing to growth. Consumption of paper grew quickly at a time when oil prices were very low. An opportunity was identified to move from natural pulp paper to a plastic based paper.
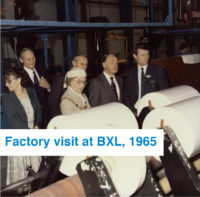
BXL review cover printed on what would become Polyart, 1967
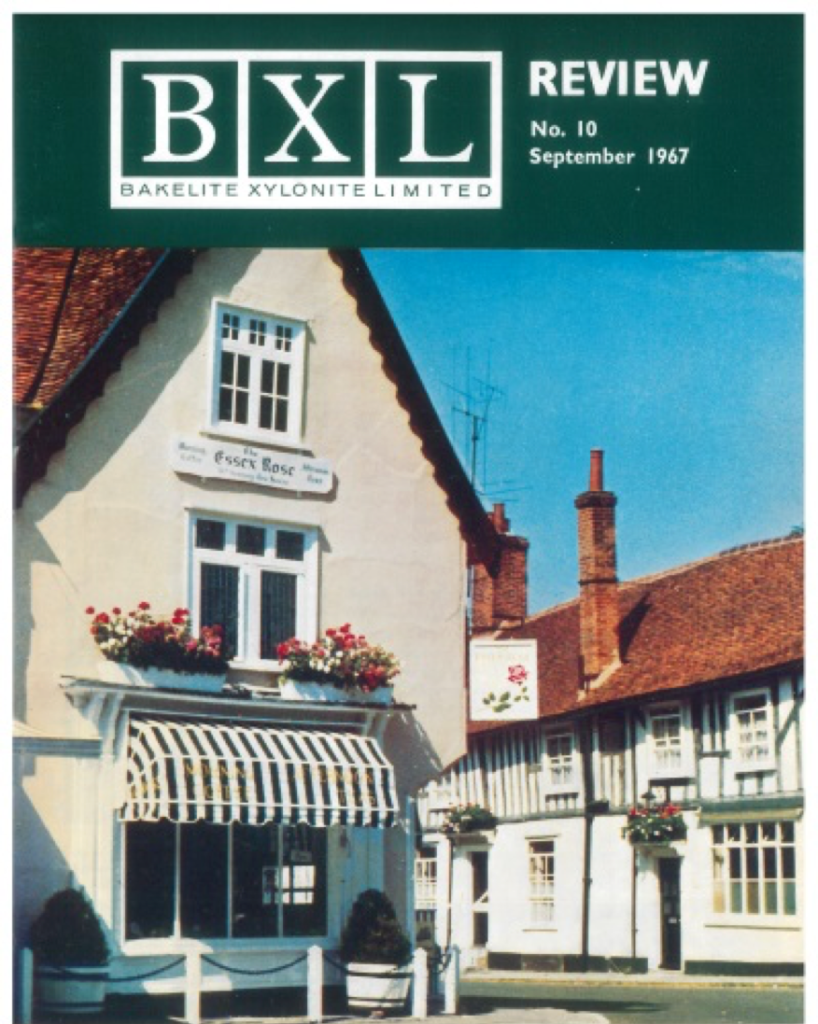
Plastic packaging companies worked on exploiting this opportunity. Firstly in Japan, because of the low levels of forestry: but also in the US, through companies such as Union Carbide.
In Europe, BXL (Bakelite Xylonite Limited), then a subsidiary of Union Carbide (later acquired by BP in 1978), developed its own version, Polyart.
FIRST STEPS
BXL had a large research centre in the UK at Lawford Place, where 1,000 scientists and engineers developed all types of plastic products including packaging films, foams, Bakelite products and plastic containers. One project, led by Dr Watson, was developing a stretched surface, treated plastic paper made from HDPE, It was called Polyart.

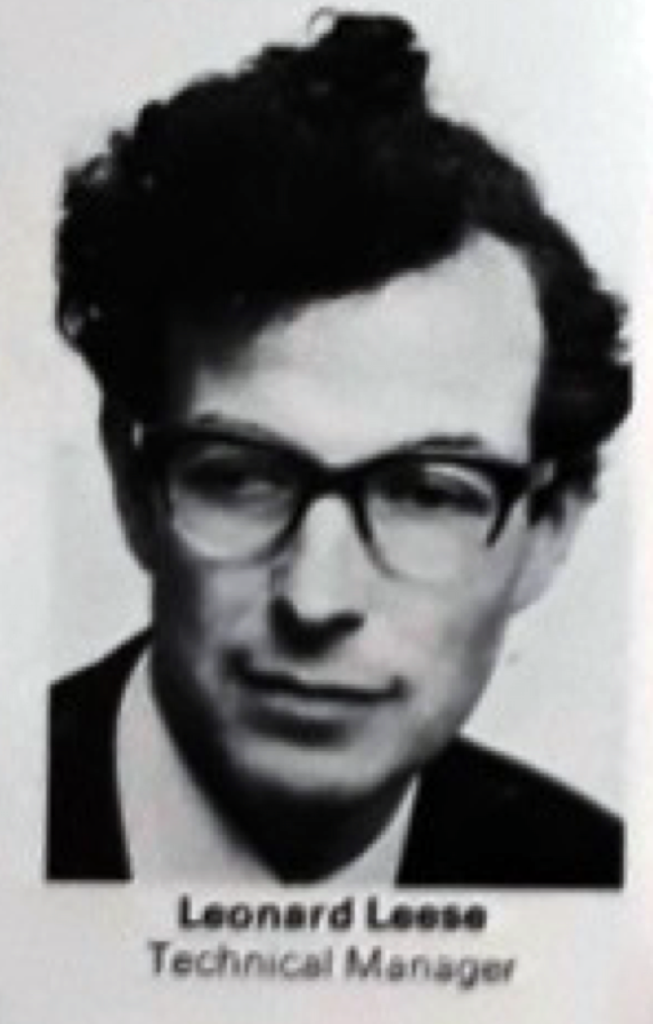
The development team was extremely enthusiastic; Dr Watson encouraged his paper customers, who were initially too shy to invest in this innovation, whilst Dr Leonard Leese, the scientist of the group, dedicated his energy in convincing his Board as to the future potential of Polyart.
The initial Polyart product was stretched on a helicoidally driven stretcher, which was soon replaced by a more sophisticated biaxial pantograph stretching technique. The resulting HDPE based film was supplied in rolls, just like paper, and it was designed to print like paper.
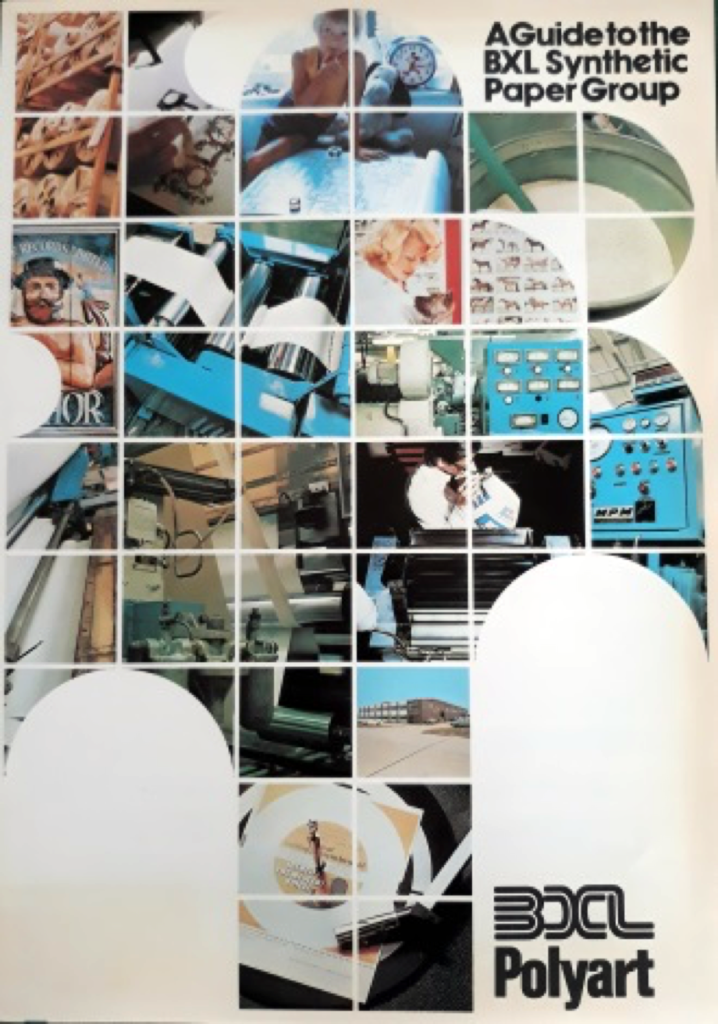
Brochure of the BXL Synthetic paper group featuring the new comer Polyart
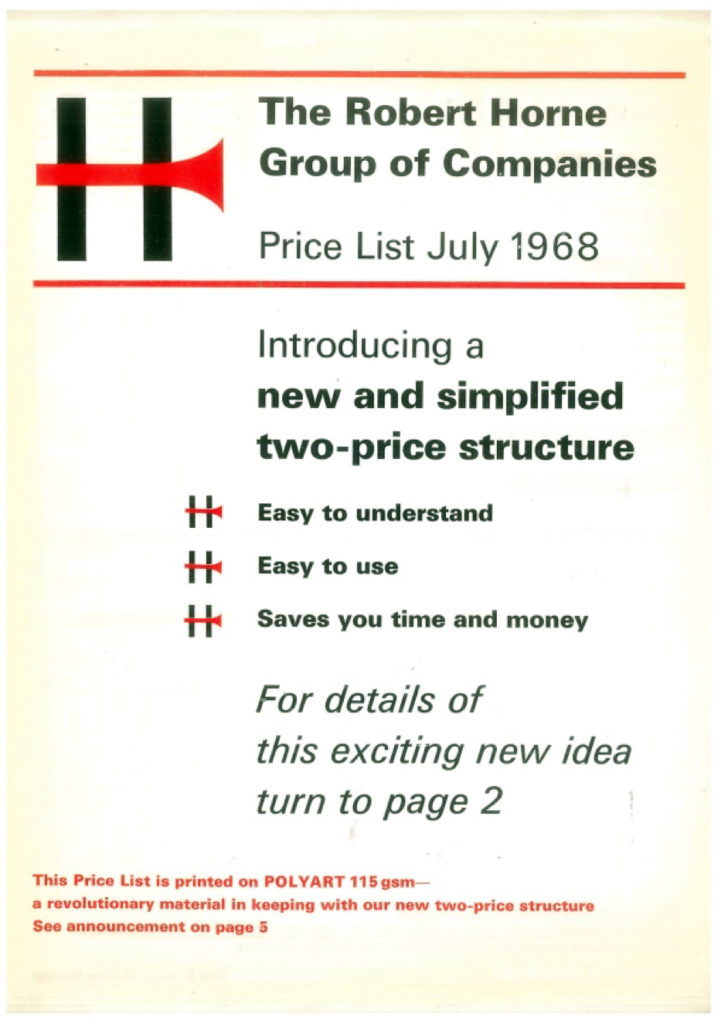
Robert Horne 1968 price list printed on Polyart
It came to the paper market in the late sixties and was sold through paper merchants all over Europe. The market was broad as the intention was to replace many different types of paper! In Japan, they even printed newspapers on synthetic paper!
In Europe, major uses were (and still are) envelopes, book covers, maps, tags, posters, business forms and labels.
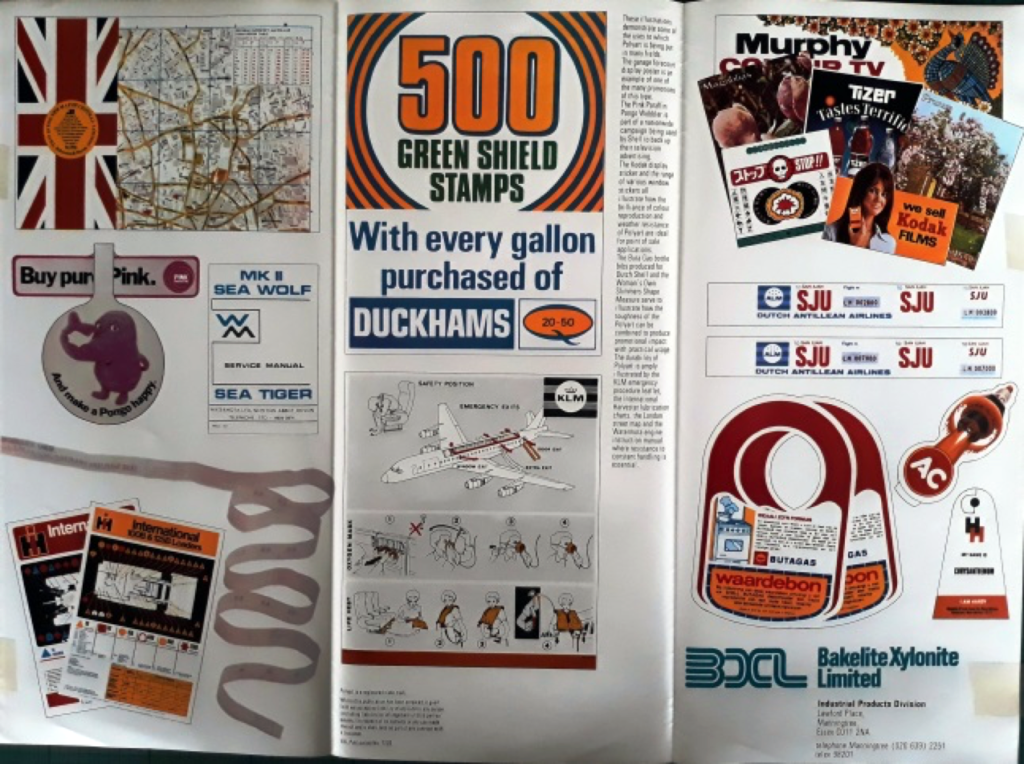
The first Polyart brochure, and already “millions of applications”
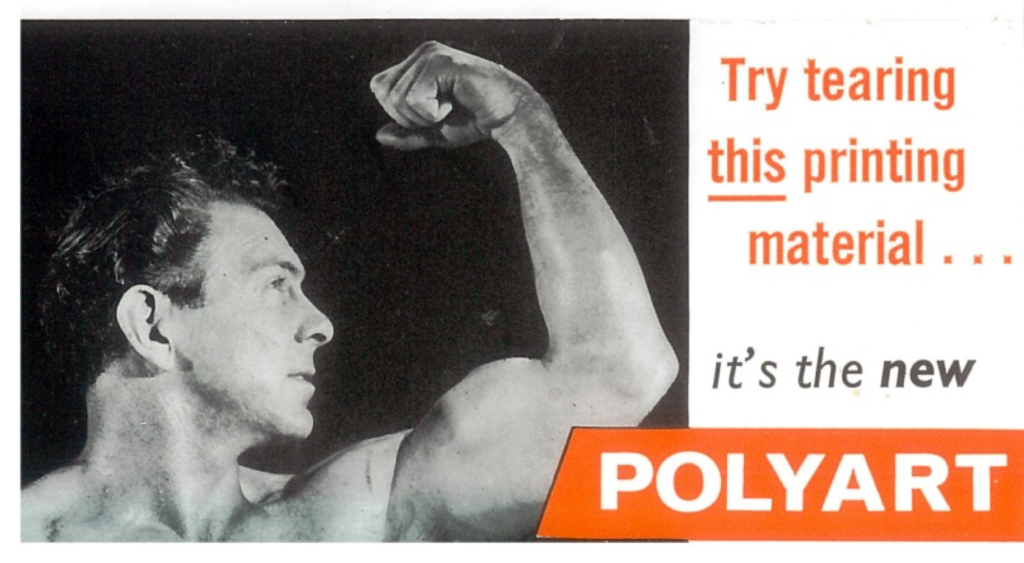
A polyart ad in 1969
Eventually, Polyart production moved to a purpose built factory at Clacton-on-Sea where the first production line was installed. In those early days, the product was not well accepted by the market because of difficulties in converting and printing, when compared with traditional paper products.
These were tough times and the embryonic business had to fight to survive throughout the early seventies.
THE SURVIVAL
The oil crisis in 1974 damaged the synthetic paper business. Only a few resisted, one of which was Polyart. The Polyart business changed strategy in various ways:
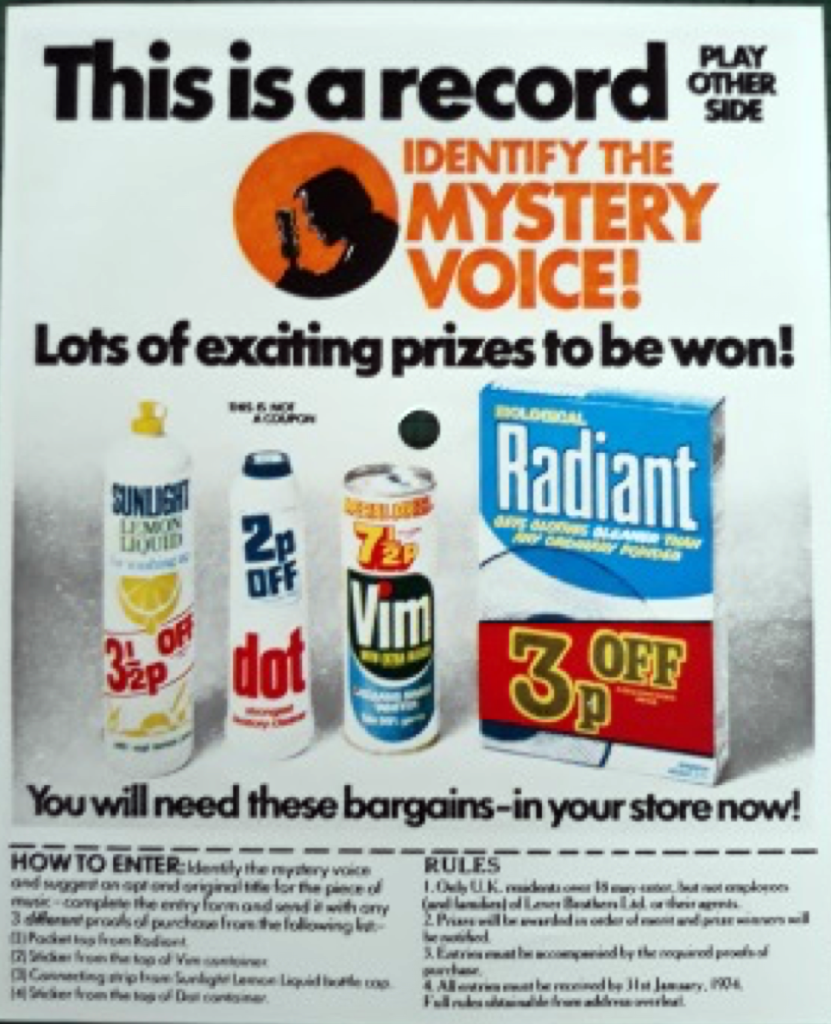
1974, a Polyart record. Lever brothers pressed 10 million copies
As oil prices were going through the roof, the product became less financially competitive but survived in specific uses like tags, labels and maps, where paper could not do a good job and customers were prepared to pay a premium.
To compensate for the increasing raw material cost, BXL invented a system to reduce the density of Polyart whilst the film was being stretched. This was a voiding process in which the density was reduced during production from 1.1 g/cm3 to 0.71 g/cm3, thus resulting in lighter weight product consuming less material.
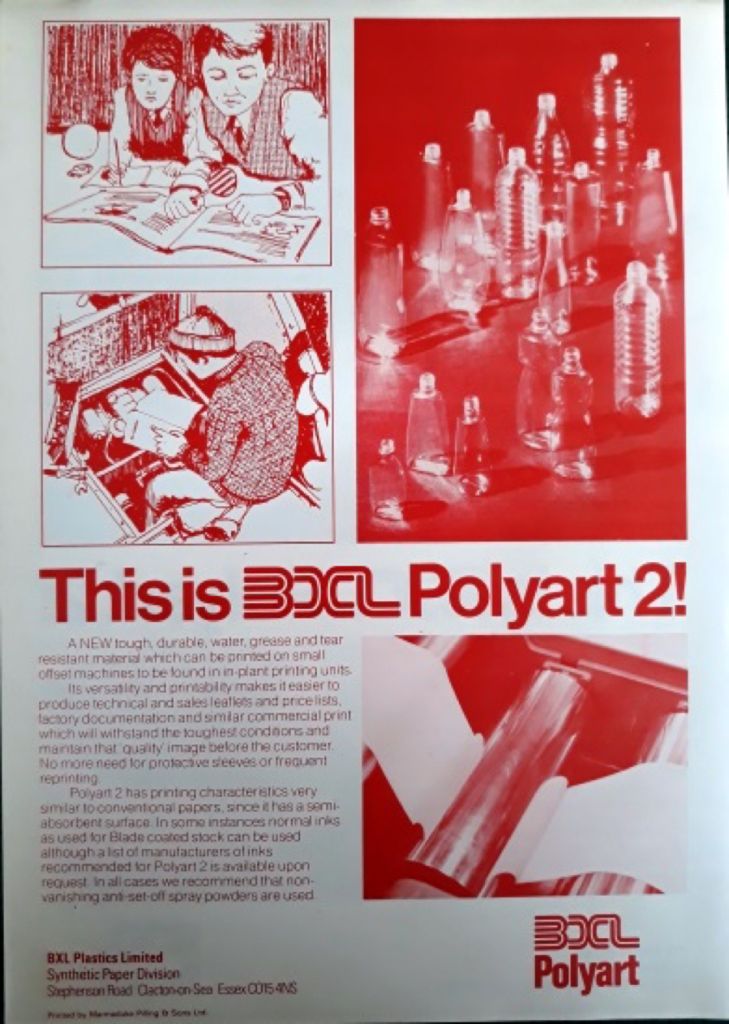
1977, first brochure of low density Polyart
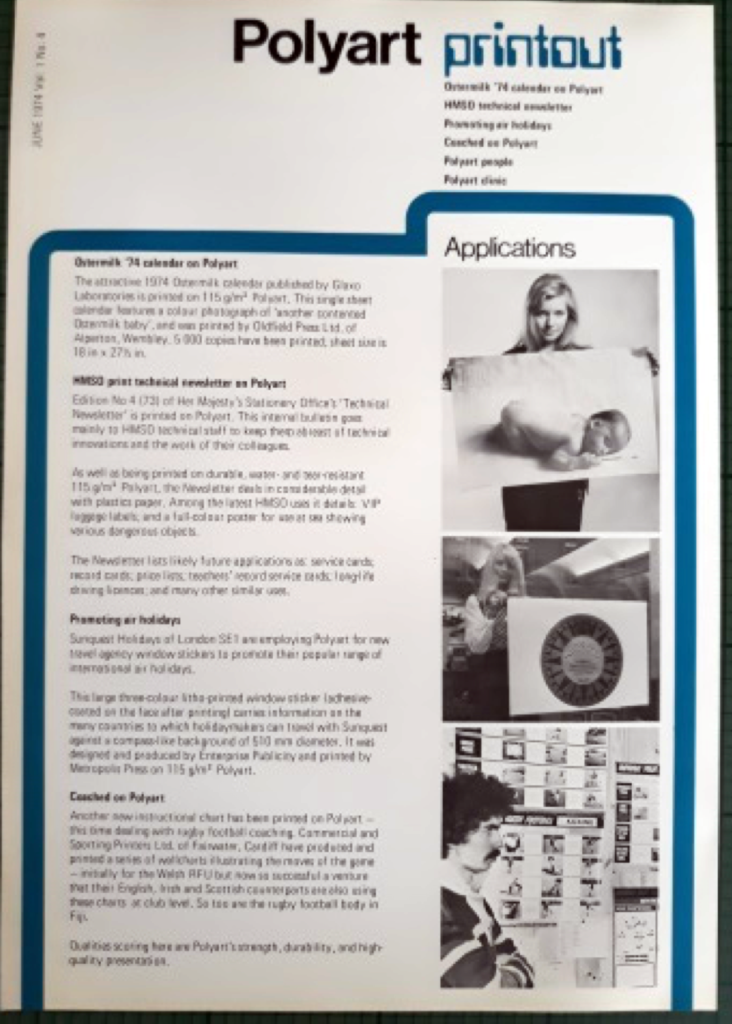
Polyart Printout presented Polyart uses
Through the 70s
This combination of specific uses and lower cost product, improved the economic viability of the business. In addition, the reduced density resulted in a product with improved compressibility, foldability and opacity, thus imparting more paper-like qualities to the plastic film.
One French paper company, Arjomari, was very famous for its speciality papers, including banknote paper, security paper, photographic paper etc… They loved speciality papers and had the right machine to coat the oriented and voided Polyart film: Polyart 2 was born with BXL producing the film and Arjomari Prioux applying the coating.
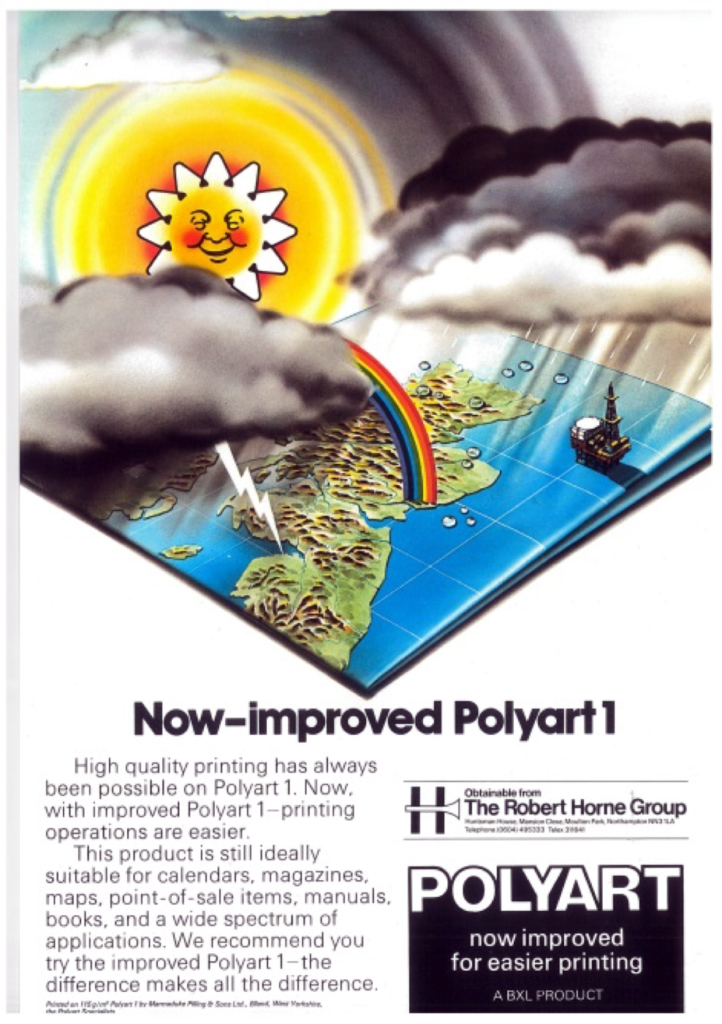
There were various evolutions to improve printability of Polyart
The final step, to get to the perfect synthetic paper, was to treat the print surface for improved printability. Different techniques were investigated and the best was found to be to coat the film on a paper coating machine, with a formulation specifically adapted for HDPE.
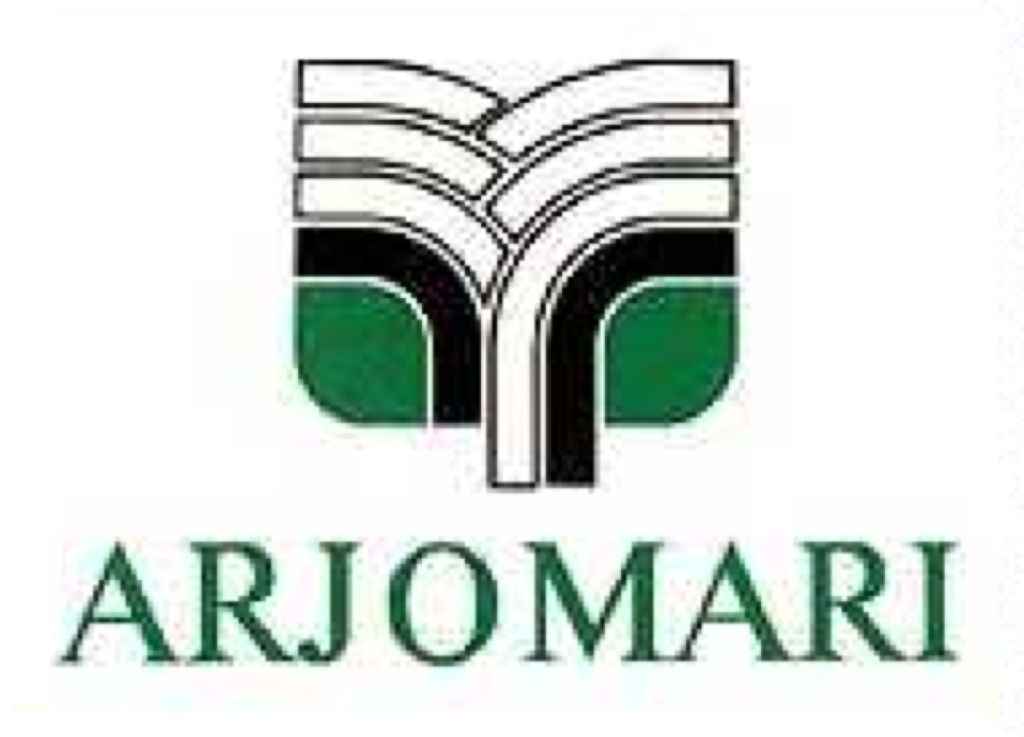
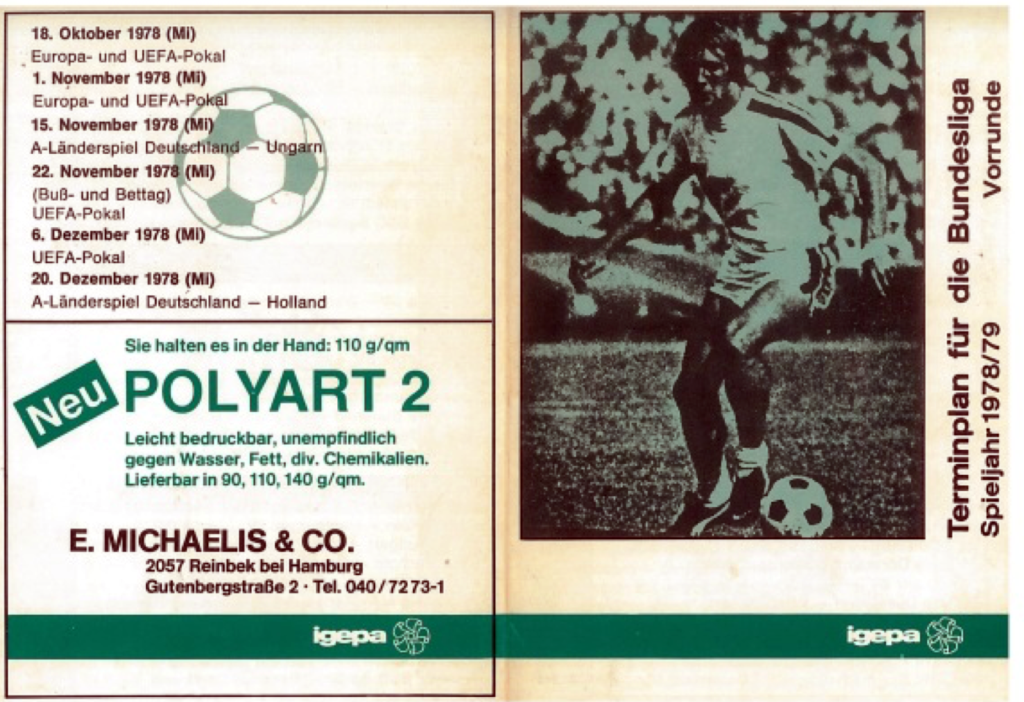
1978 Bundesliga timetable on Polyart, Michaelis Germany
With this product, BXL was now selling Polyart into the paper market and contacts with paper companies were numerous.
Large volume applications were developed quickly as Polyart 2 printed just like paper. Printers loved it! Uses opened up to food labels, technical books, folded maps, envelopes and computer printed identification barcode labels.
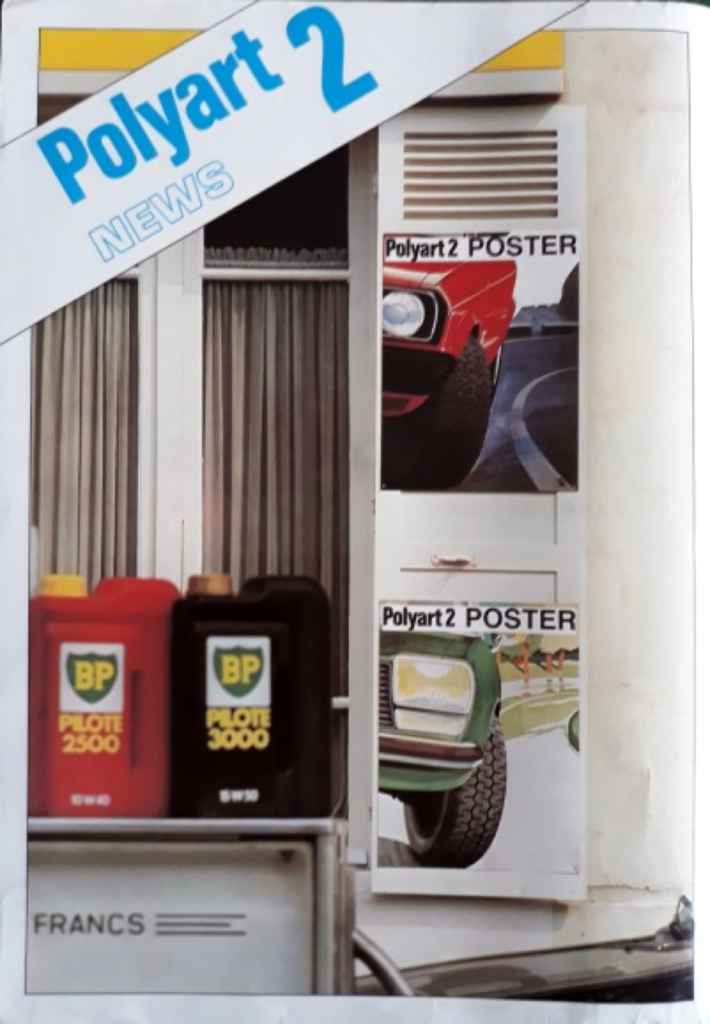
Polyart “Printout” becomes Polyart news in the 80s

Polyart International Sales contest in 1989
The business volumes were there, but the market knowledge for this plastic was still very small. Eventually, the embryonic Polyart business became a “real” business through the formation of the Arjobex joint venture, which was formed in 1981. In its first stage, Arjobex was purely a marketing joint venture.
Later, a company was created with production sites in Europe and the USA, and now Polyart is sold worldwide.
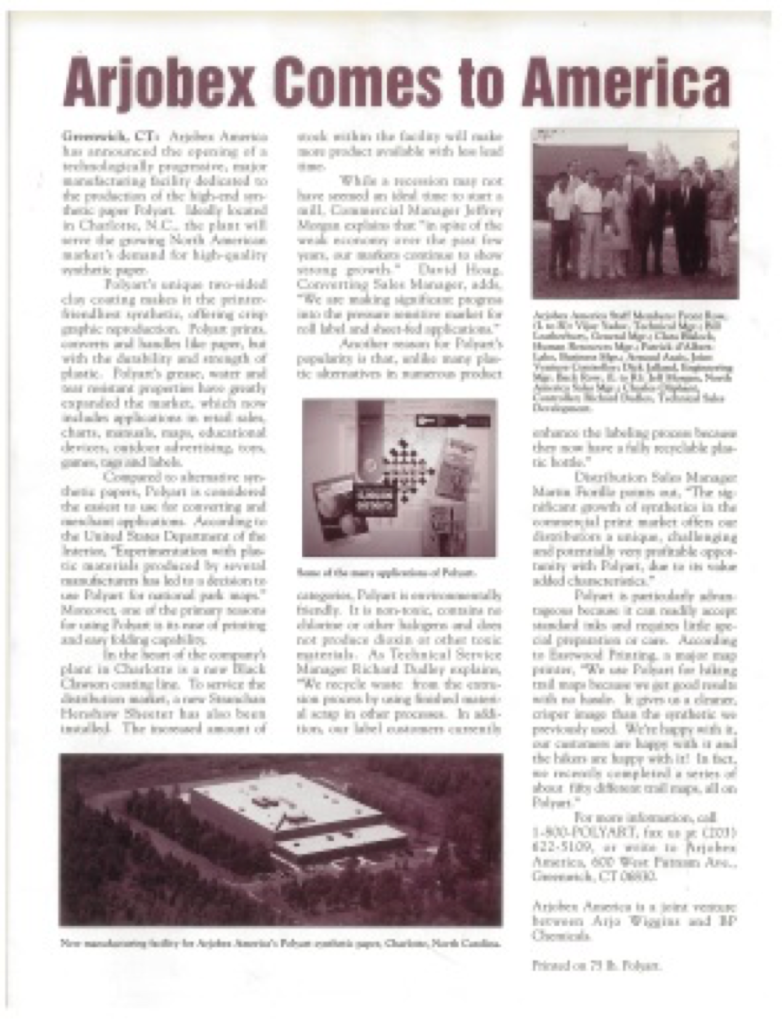
1992, Arjobex comes to America
50 Years later, Arjobex continues its growth, and has just completed a new investment to increase capacity at its historic site in Clacton on Sea. With its strategy of constant innovation, sales in more than 60 countries, manufacturing sites and R&D centres in both Europe and North America, sales offices on 3 continents, Arjobex is proud to be a preferred supplier to some of the largest Pressure Sensitive converters and printers globally, providing its customers with high added-value films, covering applications from security and industrial labels, to high end prime labelling face stock.
Arjobex places a premium on respect for the environment and is striving constantly to reduce impact on the environment to the lowest possible levels. All Arjobex production sites comply with ISO 14001 standards for Environmental Management Systems and OHSAS 18001 standards for Health and Safety.
Patrick D’Albert Lake, Arjobex CEO 1981-2009